Pack Expo 2022: Uhlmann is presenting the first bottle line for solid dose products with integrated metal detector and serialization unit
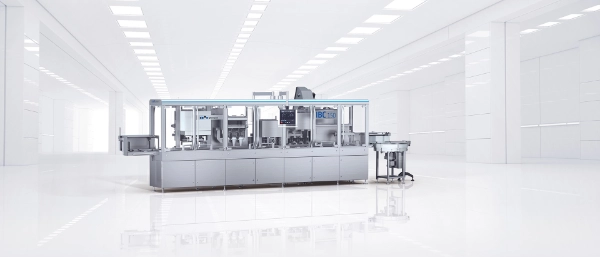
The main challenges presented by packaging solid dose pharmaceutical products in bottles are efficiency, high patient safety and seamless traceability. Uhlmann is presenting a world first at Pack Expo (October 23rd–26th) at the exhibition stand #W-13010: The first bottle line IBC 150 with integrated metal detector in a compact monoblock. The serialization unit S 500, which has been optimally adapted to the bottle line, will also be on show. With this, the total solution provider is highlighting its expertise in line machinery for bottles in the US.
Pack Expo
From bottle unscrambling to 100% correct figures, feeding of solid dose products and desiccants, sealing, labeling and serialization of bottles, this year, visitors to Pack Expo can experience the entire packaging process for solid dose products in bottles at the Uhlmann Group exhibition stand. The focus will be on the innovations in the packaging line IBC 150 – including the new bottle unscrambler BU 300, the first metal detector integrated in a monoblock, the single tablet reject function and the serialization platform S 500 for the serialization of bottles.
Bottle line for solid dose products IBC 150 for rapid product changeover
Highly automated, networked and flexible – the IBC 150 is designed to pack small to medium-sized batches of solid dose products in bottles. The monoblock line, measuring around five meters, processes on average up to 150 bottles and 24,000 tablets or capsules per minute. Rapid product changeover and short ramp-up phases also make the line attractive for CMOs, CDMOs and manufacturers of food supplements. For example, the bottle diameter can be converted to a different one in just six minutes. The entire line is controlled in a standardized manner via the user-friendly SmartControl operating system – from the new bottle unscrambler BU 300 to the Integrated Bottle Center 150 through to the serialization platform S 500.
Increased efficiency and safety when packaging solid dose products in bottles
For safe product handling and increased efficiency in the packaging process, Uhlmann guar-antees bottles are handled carefully: The new bottle unscrambler BU 300 is extremely quiet and can process up to 250 bottles per minute. The unit is easy to access and enables rapid cleaning of all surfaces.
Due to more stringent official guidelines in the USA, the content of bottles must be checked for foreign particles in the packaging process before these are sealed. Uhlmann has taken up this challenge for US pharmaceuticals manufacturers and integrated a metal detector in the bottle line IBC 150 – and it has done so without increasing the footprint of the monoblock. An-other key function of the compact line is the innovative single tablet reject function: This optional module checks the tablets already in the tablet counter and identifies any damaged or incorrect products and foreign particles. These are rejected whilst maintaining a high production speed. As only a few tablets are removed from the process instead of three completely filled bottles, as was previously the case, pharmaceutical companies can reduce the rejection rate when filling tablets in bottles by up to 99 percent.
Serialization of bottles with the S 500
As a stand-alone solution or integrated in the packaging line, the compact Uhlmann Serialization Platform S 500 is optimally adapted to the bottle line IBC 150. Depending on the challenge, pharmaceutical manufacturers can use the unit, which is free from format parts, in various configurations, e.g. for a 360° bottle inspection, for bottle labeling or serialization, whereby every bottle is identified with a 2D code. Since the code is very difficult to include on the 360° circumference of the bottle, an optional helper code can be printed on the base of the bottle. This is checked in the follow-up process and assigned to the serialization code on the bottle label.
Machine, software and service from a single source
The basis for any track & trace application is the software. Uhlmann's Pexcite platform offers a digital solution for recording, preparing and evaluating machine data – all independent of the manufacturer. At the Uhlmann Group exhibition stand, visitors can also familiarize themselves with the Pexcite platform on a line from Uhlmann's sister company KOCH Pac-Systeme. KOCH packs syringes in flexible blister packs and uses Pexcite for medical device tracking, which in turn uses the unique device identifier (UDI) to trace the medicinal products. Cremer – which is also part of the Uhlmann Group and specializes in counting and packaging solutions – will also be represented at Pack Expo. "Uhlmann’s range of Integrated Blister and Bottle packaging equipment has revolutionized the pharmaceutical packaging processes. We have seen customers focusing on Automation, Traceability and Sustainability. Uhlmann is geared to support you on any projects including Aggregation to meet 2023 deadline, converting from PVC to sustainable materials and offering Turnkey solutions." summarizes Manasvi Hegde, National Sales Manager USA at Uhlmann.